In the heart of Marietta, Georgia, the sprawling Lockheed Martin factory buzzes with activity. This is where the renowned Lockheed Martin C-130J Super Hercules, a four-engine turboprop military transport aircraft, comes to life.
The assembly of each C-130J involves around three thousand employees, highlighting the sheer scale and complexity of the process.
A Comprehensive Update: The C-130J Super Hercules
The C-130J represents a significant evolution of the original Lockheed C-130 Hercules. It boasts new engines, an advanced flight deck, and updated systems, making it the most modern version of the Hercules family. As the only model currently in production, the C-130J is a cornerstone of military transport, with approximately 600 aircraft delivered to 27 operators across 24 countries as of recent reports.
The Assembly Process
At the Marietta factory, the assembly begins in a vast hall where individual components, sourced from various sub-factories, are meticulously put together. The parts range from the smallest machined pieces to large modules that are assembled on-site. High-performance CNC milling machines ensure precision in manufacturing intricate aircraft control parts.
Systems and Final Assembly
The assembly process is intricate and highly coordinated. Systems installation technicians are tasked with integrating hydraulic, electrical, and other essential systems into the aircraft’s frame. This work requires careful sequencing, especially given the confined spaces within the aircraft.
The wings, one of the few major components manufactured entirely at Marietta, are a critical part of the assembly process. They are prepared first, followed by the attachment of the Rolls Royce AE 2100 engines and propellers.
Quality Control and Testing
Quality control at Lockheed Martin is rigorous. Each C-130J undergoes multiple inspections throughout the manufacturing process to ensure it meets the highest standards. After assembly, the aircraft is moved to a special hall for painting.
For instance, a Royal Air Force C-130J recently received a special livery to commemorate the 50th anniversary of the RAF’s first C-130 Hercules. This process involves detailed planning and computer-aided design to meet the specific requirements of each customer.
Civilian Variant: The LM-100J
Alongside the military C-130J, the Marietta plant also produces the civilian variant, the Lockheed LM-100J. This version is tailored for commercial transport and other civilian applications, with 115 aircraft in service worldwide.
The LM-100J benefits from the same advanced technology and robust design as its military counterpart, making it a versatile addition to any fleet.
Training and Certification
Lockheed Martin’s Marietta facility includes a Hercules training center, where pilots receive simulator training to prepare for flying these complex aircraft. Before delivery, each C-130J undergoes extensive test flights and trials. Experienced test pilots, who bring decades of piloting experience, evaluate the aircraft’s performance, ensuring it meets all operational requirements.
Global Impact and Capabilities
The C-130J Super Hercules is designed for a variety of roles beyond transport, including troop deployment, medical evacuation, search and rescue, and aerial refueling. Its ability to operate from unprepared runways makes it an invaluable asset for military forces worldwide.
With a maximum range of around 4,500 kilometers and a top speed of approximately 660 kilometers per hour, the C-130J is a testament to modern engineering and design.
The Airbus A400M: A European Counterpart
While the C-130J remains a dominant force in military transport, the Airbus A400M serves as a notable European counterpart. Bridging the size gap between the C-130 Super Hercules and the larger C-17 Globemaster, the A400M offers enhanced payload capacity and the ability to use rough landing strips.
It performs multiple roles, including aerial refueling and medical evacuation, with advanced capabilities that make it a strategic asset.
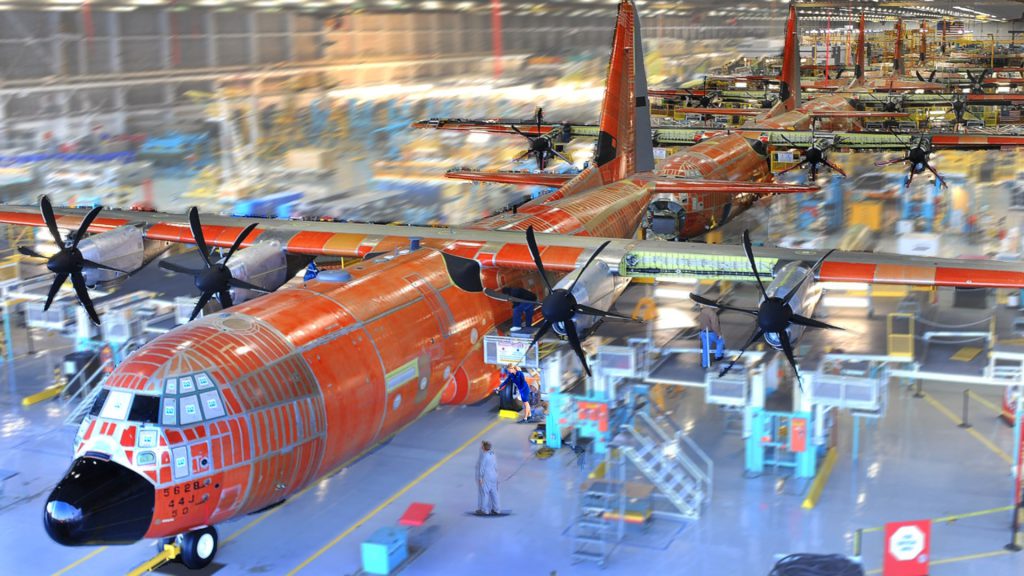
Production and Capabilities
The Airbus A400M is produced in various European factories, with major components like the fuselage constructed in Bremen, Germany, and Spain. The aircraft features a blend of aluminum alloys and composite materials, ensuring strength and durability.
Its full glass cockpit is equipped with state-of-the-art avionics, providing pilots with comprehensive control and situational awareness.
Strategic and Tactical Versatility
Capable of carrying up to 37 tons, the A400M combines strategic and tactical airlift capabilities. It can operate from small, unprepared airstrips, making it ideal for rapid deployment in disaster relief and military operations.
The A400M’s performance in range, speed, altitude, and payload capacity surpasses that of previous-generation tactical airlifters, delivering game-changing capabilities to its operators.